AAA weekly
2019-10-15
Copyright FOURIN, Inc. 2025
Futaba Cold Forming of Body Frame Parts Using 1.5GPa Material
Futaba Industrial is proceeding with the development of body frame parts using cold forming technology for tensile strength of 1.5 GPa class ultra-high-tensile materials. The company is aiming for mass production from 2022–2023.
The use of hot stamping is increasing, especially in Europe, for forming ultra-high-tensile materials. On the other hand, although cold forming poses issues in terms of formability, it has advantages over hot stamping such as low CO2 emission and better production speed. Futaba Industrial intends to reduce weight of vehicle bodies by cold forming and promote CO2 reduction in life cycle assessment.
In general, cold forming of ultra-high-tensile material is greatly affected by spring back, making it difficult to ensure dimensional accuracy. To address this issue, Futaba Industrial has focused on improving the accuracy of molding simulation. Parameters such as material tensile test data and material property values were reflected in the simulation, and the matching ratio between actual molding and simulation was increased by adjusting the parameters independently.
As a result, Futaba Industrial was able to accurately grasp the complex stress state generated inside the material during molding and optimally control the residual stress in each part. In this way, the company succeeded in securing dimensional accuracy by cold forming of ultra-high-tensile material.
Futaba Industrial is also collaborating with several Japanese steel manufacturers in the development of cold forming technology. 1.5GPa-class ultra-high-tensile materials vary in material properties. Futaba Industrial evaluates and compares materials procured from multiple steel manufacturers and provides feedback to each steel manufacturer. In addition to this, Futaba Industrial is also cooperating with steel makers in simulations and at molding sites. These efforts make it possible to improve dimensional accuracy by performing stress analysis and enhance countermeasures according to the properties of the materials provided by each steel manufacturer.
Futaba Industrial attaches great importance to cold forming, but also has know-how in the area of hot stamping. In anticipation of growing demand for future lightweight and high-strength vehicle body parts, the company intends to meet customer needs by using both cold forming and hot stamping, adjusting technology to the required material strength, molding shape and scale of parts supply.
Futaba Industrial: Developing Cold-formed Car Body Parts Using High-tensile Material with Tensile Strength of 1.5 GPa
Based on interviews with Takuhisa Inagaki (Managing Executive Officer, General Manager of Production Engineering Division), Yutaka Yamada (General Manager of Body Development Department) and Kazuhiro Kawakita (Director of Body Development Division, Body Development Department) at Futaba Industrial’s Takahashi Factory (Okazaki City, Aichi Prefecture) on July 8, 2019Recent high-tensile technology for car bodies
In recent years, European body parts manufacturers have brought hot stamping technology into Japan that can mold 1.5GPa materials. Hot stamping is a technology that increases strength from low-strength steel sheets and has been used in Europe for a long time. However, hot stamping reheats the material once heated, resulting in a large energy loss during molding and a large amount of CO2 emissions. The production speed is also relatively slow.
On the other hand, cold forming can reduce CO2 emissions in the production process and production speed is faster than hot stamping. The small amount of CO2 emitted is also very important from the viewpoint of life cycle assessment (LCA), which has attracted attention in recent years.
However, cold forming is difficult. Outside Japan, there are few cold-formed materials even in the 980 (tensile strength 980 MPa) and 1.2 GPa (1,180 MPa) categories. Cold forming is Japan’s world-class advanced technology.
Cold-forming body frame parts with a tensile strength of 1.5 GPa
Futaba Industrial has recently developed a technology for cold forming (pressing) car body frame parts using ultra-high tensile materials with a tensile strength of 1.5 GPa (1,470 MPa).
Cold forming is a craft of Futaba Industrial, and so far cold forming of 980 and 1.2 GPa materials has been realized. Based on the know-how the company’s has accumulated, it succeeded in cold forming 1.5GPa material, which has the same strength as European hot-stamped materials. Futaba Industries made prototypes of front pillars, center pillars, rocker outers (side sill outer panels), roof rails, and other products, using cold-formed ultra-high tensile (1.5GPa) materials. The company aims for mass production from 2022-2023.
Difficulty of cold forming

Futaba Industrial’s cold-formed front pillar is integrally formed up to the front window’s front pillar. Integrated molding has a great advantage in terms of production efficiency, but it is difficult to achieve dimensional accuracy during molding.
This is because, in particular, a curved portion such as a corner portion of a pillar has a flange called tensile flange, which is subjected to tensile stress, and there is a risk that a crack may occur in the portion. It is important to control the movement of the material during molding so that cracks do not occur.
The center pillar also has an extended flange at the curved portions at both ends of the lower part, and is molded so that cracks do not occur. Furthermore, the center pillar has a shape curved toward the inside of the vehicle body from above. This part also has a risk of camber back (a kind of spring back) that curves to the outside (reverse side) of the vehicle body after molding.
The roof rail is elongated and has low rigidity, so there is a risk of twisting. Furthermore, in order to bend according to the shape of the roof, it is necessary to control the stress in consideration of both the twist and the curved portion.
Development of processing methods suitable for ultra-high tensile materials
Super high-tensile material has little elongation and is easy to break. 1.2GPa materials have only 8-10 percent elongation and 1.5GPa materials have even less.
Regarding spring back, when strength is increased, the elastic deformation characteristic remains even after plastic processing, the amount of spring back increases compared to mild steel plates. For this reason, in order to mold with high dimensional accuracy, it is important to control the residual stress of each part of the component.
Futaba Industrial uses stress control technology from the stage of forming 980 materials. For example, when a hat-shaped part is formed, a method called “surface trimming method” is adopted. Regarding the chamfering method, bending is performed in the first step, and the bent portion is crushed in the next step (the ridgeline is crushed: the shape is chamfered). As a result, tensile stresses in opposite directions are applied to the outer side and the inner side of the bent portion, respectively, so that the stress affecting the spring back is offset and accuracy is improved.
However, 1.2GPa and 1.5GPa materials have high strength and it is difficult to crush the bent part, so a method called “shift bending” is adopted as a countermeasure. The shift bending is a technique in which bending is performed at the first step slightly outside the original bending position first and then formed into a product shape in the next step.
As for the conventional construction method, the tensile stress concentrates only on the outside of the bent portion, generating spring back. When the shift bending method is used, in addition to the tensile stress to the outside of the material, a tensile stress (spring go) is also generated on the inside due to the bending return effect of the first-step bending. Thereby, since stress can be canceled, the precision at the time of shaping improves.
Countermeasures for cracks / wrinkles during parts molding
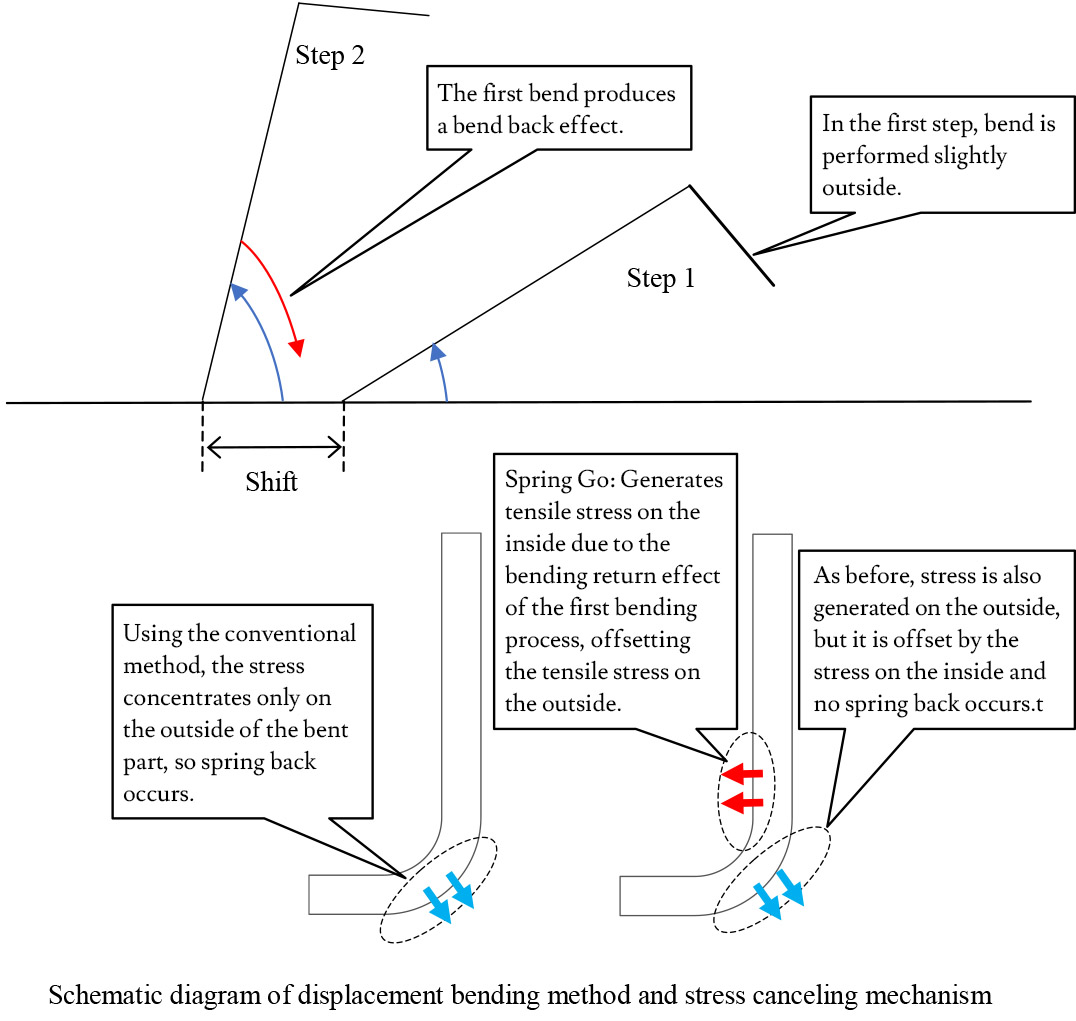
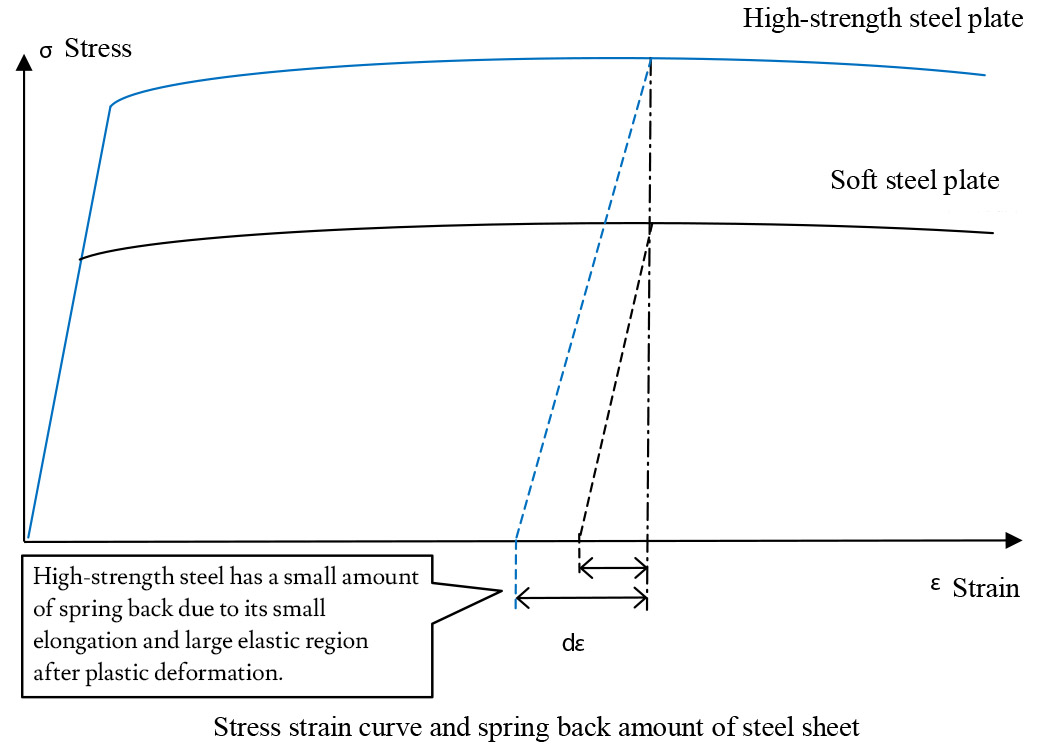
As for cold forming of super high-tensile materials, Futaba Industrial incorporates residual stress control into the first two to three steps to suppress spring back and ensure dimensional accuracy during molding.
With mild steel plates, even if spring back occurs after forming, accuracy can be ensured by looking inside the mold. However, in the case of ultra-high tensile materials, the spring back is too large, so the stress is controlled during molding to increase accuracy.
In addition, the countermeasure against wrinkles generated during molding is determined by how much the product can be restrained during molding. However, if the restrain is too strong, the flow of material into the mold is suppressed, causing cracking. For this reason, it is important to optimize the pressing force at the time of restraint.
In addition, there is a means of controlling wrinkles by controlling stress with the right product shape design. For example, a pinch is added to the lower curve of the center pillar or the front pillar.

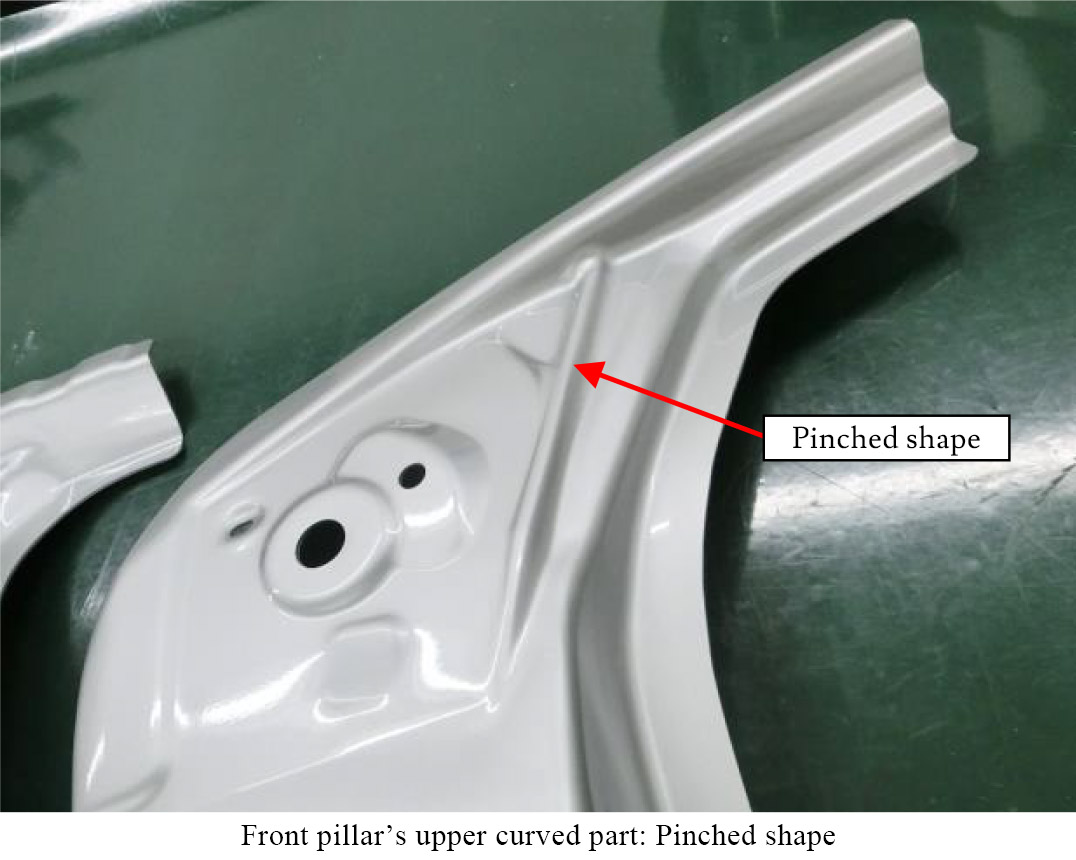