AAA weekly
2019-12-02
Copyright FOURIN, Inc. 2025
Development Issues, Design Direction of Next-gen Electric Axles
Mass-market BEVs will be released on a global scale, expanding market feedback and needs for BEV development. FOURIN has interviewed a powertrain development consultant who is an expert in transmissions and familiar with global market trends regarding the technical requirements for e-axles (mechanical and integrated drive units consisting of motors, inverters and gears) to advance to the next stage.
This report examines the needs and methods for multistage gears as well as shaft and bearing torque requirements, lubrication and thermal management, NVH, weight reduction, durability and energy regeneration.
Using CVTs and two-stage gearboxes for E-axles have various advantages for such as improved fuel efficiency. Proposals for two-stage gearboxes are increasing, but have yet to become mainstream.
Whether the motor and driveshaft use coaxial or parallel gear depends on the mounting and layout of the drive system. Regarding torque requirements, the torque applied from the gear set to the driveshaft is not much different between an engine vehicle and an E-axle-equipped vehicle (BEV). On the other hand, torque demand on bearings becomes more severe with BEVs due to the use of large drive motors. The suitable bearing type and its material is selected according to conditions of use based on cost, durability, size, weight, friction and other factors. Similarly to gears, lubricating oil for motors will be tailored to motor characteristics and market needs.
E-axle NVH is dealt with in advance in order to avoid noise and resonance. The mount has also been newly designed to reduce noise by optimizing the entire system.
With regard to weight reduction and durability, safety is a major concern. Companies aim for the best results with cost and effect in mind.
Overall, energy regeneration is important for improving electricity costs. High efficiency of the inverter and the overall design is the key. The manufacturer’s knowhow will set its product apart from that of other companies.
Direction of Next-generation E-axle Development
Anonymous interview with a powertrain development consultant familiar with the global market
Next generation E-axle Gears: Adopting Multistage System and Type Requirements
Need for Multistage Gears
The E-axles that have been commercialized so far are nearly all single-stage decelerators. This is because, as a feature of the motor, torque can be generated from a stopped state, and it can generate high torque with low rotation. There are proposals for using stepped CVT, but it has not become mainstream yet. Nearly all stepped gears are two-stage gears.
Coaxial or parallel gear?

Depending on mountability and the drive system, the motor gear and driveshaft gear can be either coaxial or parallel.
For example, when trying to attach a motor to the center of the engine in the engine room, it is difficult to arrange the driveshaft coaxially. You may raise the position of the driveshaft a little, but if you bring the motor there, its lower part will collide.
One of the issues is whether coaxial or parallel is good in terms of mountability. It really depends on the motor’s position, the overall layout and the vehicle’s drive system (front-wheel drive, rear-wheel drive, four-wheel drive, in-wheel motor, etc.).
In-wheel motor technology requires a coaxial gear
Parallel layout requires a multistage gear
When gear shifting is considered with parallel shafts, gears corresponding to the number of stages are required. Similarly to MTs, there are as many gear trains as the number of gears, and ways to switch between them.
However, it is impossible to add an MT to a BEV, so a common and synchronized transmission mechanism is required for the clutch. There are methods such as using a dog clutch, but there are problems such as torque loss.
Inertia is also a problem. We want to use the rotational inertia energy of the motor to reduce motor rotation.
There is a loss of inertia energy if you try to shift without a shock. CVT is advantageous in this respect.
There is an electrical loss even when regenerating. It is necessary to design the speed change mechanism by calculating the overall gain and loss.
Romax and others are calculating gain and loss. Gear makers have that know-how in the first place.
E-axle torque requirements: drive shaft and bearing
Torque does not change even with BEV
Whether the torque applied to the driveshaft from the gear set varies depending on whether it is an engine vehicle or an E-axle equipped vehicle (BEV).
Although a difference in moment of inertia can be made at the time of transition, in the case of both BEVs and engine cars the power is eventually transmitted to the road surface through the tires. For this reason, the torque in the driveshaft is the same for both vehicle types. When the horsepower (output) is the same the torque decreases as the same horsepower is obtained at high rotation. The torque at a motor speed of 20,000 rpm is smaller than the torque at an engine speed of 8,000 rpm. The driving force of the tire is the torque of the driveshaft. Once the driving pattern is determined, the torque applied to the tire is basically the same for both engine vehicles and BEVs. If the BEV accelerates faster, the driveshaft’s torque will increase accordingly. For example, in the case of a sports car, the acceleration is 1G and the normal time is 0.6G. For ordinary cars, 0.2G is usually sufficient. However, it is necessary to set acceleration at about 0.3G. It should not be set so that it cannot cope with acceleration when turning right or avoiding dangerous situations. In this way, the torque required for the driveshaft is determined in accordance with the acceleration. Whether the motor torque is high or low, the driveshaft torque will be the same.
In conclusion, if the driving pattern is the same, the torque applied to the tire (driveshaft) is constant for both engine cars and BEVs. This means that the torque requirements for the driveshaft via gears will not change.
E-axles call for stricter motor and gear shaft requirements in terms of lubrication
The first requirement is that the motor rotates very fast, which makes lubrication difficult. While oil drop lubrication was sufficient enough in the past, E-axle technology requires oil jet lubrication.
Compared to an engine car, BEV speed is high (high rotation), so the shaft needs to be rigid. However, it does not mean that the shaft’s material has to be changed. Rather, the torque becomes smaller at higher speeds, so the shaft can be thinner. However, when it comes to high speed, the problem of heat comes up.
Extreme demand on large-drive motor bearings
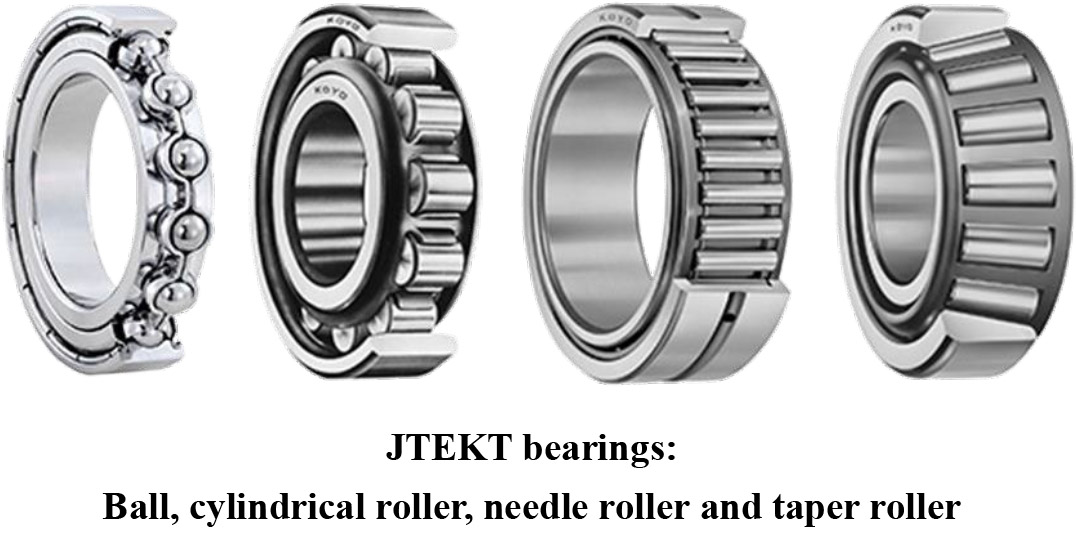
Demands on bearings are becoming stricter. The bearing cage is naturally subjected to centrifugal force. There are many planetary gears that can be combined with the engine that rotate at 10,000-15,000rpm. However, the bearings used are generally small. On the other hand, the E-axle is as big as the main motor that moves the car. So, large bearings are also required.
As for the motor, the specifications of the bearing are determined by the diameter x rotation speed (dn value) and transmission torque. If the diameter is small, there is no problem even at high rotation. However, the dn value increases as the rotation speed increases because the shaft diameter is large.
On the other hand, the centrifugal force (G) cannot be reduced so much by increasing the rotation speed. Therefore the magnitude of the centrifugal force becomes very difficult because it comes to the square of the number of revolutions.
Each unit uses a bearing according to the output direction
Mainly, three types of bearings are used for transmissions ball bearings, cylindrical roller bearings and needle bearings. Some of them also use tapered roller bearings.
The most commonly used type is ball bearing. This is because its price is low. Although it is expensive, cylindrical rollers are used for those with a large radial load. Needle rollers are used for high-speed rotation and small loads. Needle rollers have a small diameter and cannot withstand high loads.
Normally, a ball bearing is used for a motor, but in the case of a parallel gear a roller may be required to support it. In the case of a roller, since ball bearings cannot receive axial force, tapered roller bearings are used. However, the use of tapered roller bearings increases cost.
In the case of a gear, if it has parallel teeth, rattling occurs which generates noise. For this reason, helical teeth are used. In this case, power comes out in a radial direction. Cost drops, if force can be received with a ball bearing using helical teeth. Since the direction of the force received is generally determined, sometimes cylindrical roller bearings are used.
First, you must decide how much you want to spend on one unit. Transmission manufacturers take into consideration cost, durability, size, weight, friction and other factors to determine cost.
Please
register or subscribe to view this report for free.
If you’re already a subscriber, sign in.
Credit card information is not needed for free trial registration.
You are eligible to view one report for free.
Additional reports require subscription.