AAA weekly
2020-02-03
Copyright FOURIN, Inc. 2025
Hitachi Zosen Promotes Methanation to Realize Carbon Neutral Operations
Realizing a decarbonized society in 2050 is a major challenge for the transport sector. From the viewpoint of life cycle assessment, which considers everything from production to disposal / recycling, there are expectations to reduce total carbon dioxide emission including the energy conversion, industrial and household sectors.
One of the issues that has attracted attention recently is the methanation technology that produces methane by reacting hydrogen and carbon dioxide. Japan’s Prime Minister Shinzo Abe mentioned methanation at the World Economic Forum in January 2019. Following the Prime Minister’s speech, the Ministry of Economy, Trade and Industry and the Ministry of the Environment have begun full-scale R&D support of methanation.
Methanation is a technology discovered by a French chemist in the early 1900s. In 1995, Koji Hashimoto of Tohoku University (currently Professor Emeritus of Tohoku University, Tohoku Institute of Technology) demonstrated for the first time in the world that carbon dioxide can be captured and reused (carbon recycling), using a simple equipment on the rooftop of the Russia has realized, is possible with little energy loss. Locations where renewable energy can be used efficiently are unevenly distributed around the globe, so it is best to conduct methanation locally and transport it as methane to the consumer. The biggest barrier to the spread of methanation is the electricity cost. There is an inherent problem with Japan’s energy policy, so renewable energy prices are unlikely to fall. Kumagai recommends seeking renewable energy overseas, converting it to methane and transporting it consumer. Alternatively, another recommended method is renewable energy providers provide users energy directly without connecting to the grid.
Since methane generated using renewable energy leads to direct reduction of carbon dioxide, methane derived from renewable energies should be certified as “premium methane” by a system such as FIT to promote its use.
Mr. Kumagai believes that the Sustainable Development Goals (SDGs) set by the United Nations in 2015 will support the spread of methanation. The reputation of international companies is changing from mere financial indicators to those that include the SDGs. One of the biggest bottlenecks in the industry’s approach to the SDGs is carbon dioxide emissions from transportation vehicles. The automotive industry should take that challenge seriously.
Methanation: Effective and Simple Method to Reduce CO2
Based on an interview with Naokazu Kumagai (Consultant at Industrial Equipment Business Unit, Machinery Business Headquarters, Hitachi Zosen Corporation) at Hitachi Zosen Corporation’s Kashiwa Office (Kashiwa City, Chiba Prefecture, Japan) on July 24, 2019Relationship between internal combustion engine and synthetic fuel (E-fuel / E-gas)
Even if BEVs expand their presence in the market (20% at most), internal combustion engines will remain for years to come. Many automotive industry professionals think so. German automakers who appear to make a big fuss about the adoption of electric vehicles are in fact focusing on internal combustion engines. German manufacturers are firmly confident that the world’s leading German technology is the internal combustion engine and will not give up their competitive edge. Audi is one such car manufacturer. They protect their advanced internal combustion engine technology which they have cultivated so far and conceive ways to utilize it. The result of their effort is synthetic methane (E-gas). Water is electrolyzed using renewable energy (hydropower, wind, sunlight, etc.) to produce hydrogen (H2). When hydrogen is artificially made to react with carbon dioxide (CO2) methane (CH4) is produced. This methane is almost the same as natural gas and can power a CNG (compressed natural gas) vehicle. The technology for artificially producing methane from hydrogen and carbon dioxide is called methanation. It is an old technology discovered by the French Nobel prize chemist Paul Sabatier in the early 1900s. Now, it is regaining attention as a breakthrough technology that increases the use of renewable energy while keeping the internal combustion engine on the market.Mechanism of Audi’s g-tron and e-gas
Audi calls the g-tron a bi-fuel engine that can run on both CNG and gasoline fuel. This approach is interesting. Audi distributes g-tron users a card called Audi e-gas Tankkarte (e-gas tank card). When the user goes to the gas station with the e-gas tank card to buy CNG, the filling information is sent to Audi's management center. Audi will inject as much e-gas into the CNG supply network as used by g-tron users. In other words, the user fills the g-tron with ordinary CNG which contains a small amount of e-gas, but Audi’s theory is that the user fills the g-tron only with renewable energy. Even if the actual fuel does not contain much gas derived from renewable energy, the theory is correct if judged only by the balance of the entire gas supply network. And the more users use CNG with e-gas tank cards, the more they help reduce carbon dioxide.Almost fully-automatic Audi e-gas plant
The Audi’s e-gas plant in Werlte, Germany operates almost fully automatically. There is only one person in charge, and even that person stays at a distance of about 10 minutes by car at night. When a problem occurs at the factory, the person in charge receives a smartphone notification. The ability to do most of the work fully automatically demonstrates that methanation is an easy process.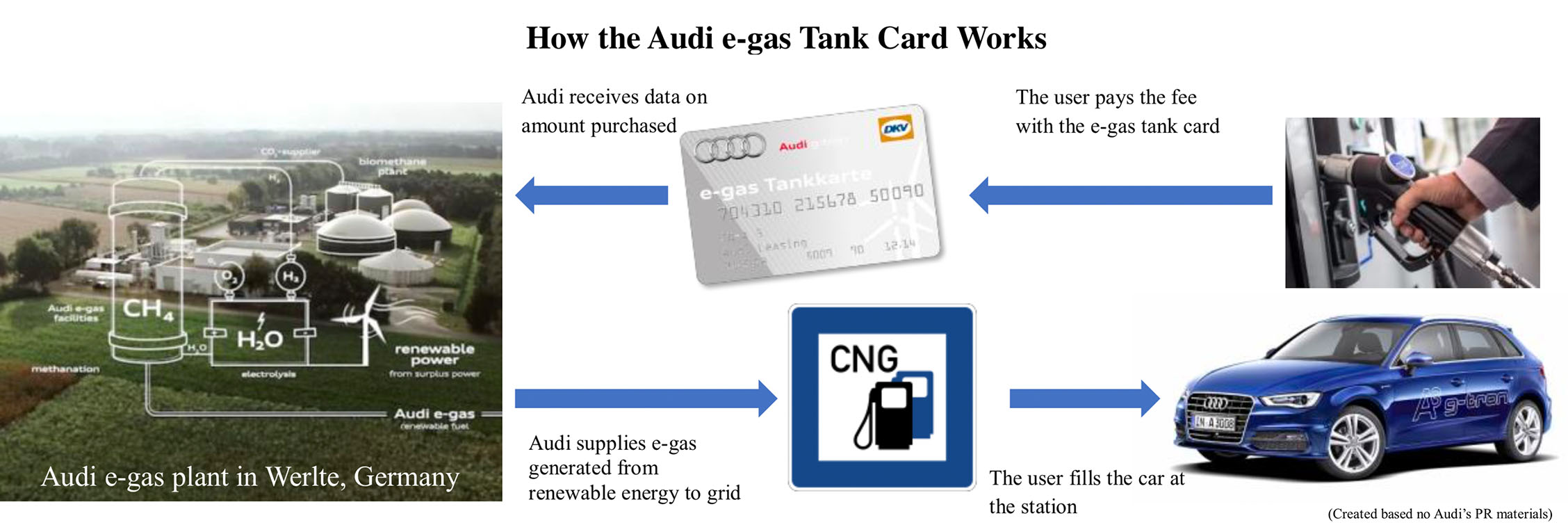
Power supplied to Audi e-gas plant from the grid
The Audi e-gas plant can produce up to 325 Nm3 (normal cubic meters) of e-gas per hour. Audi officially claims that it produces hydrogen by electrolyzing water with renewable energy. However, the electricity used here is not directly derived from renewable energy. In fact, Audi gets its electricity from the grid (power supply network). This is because the output of renewable energy is unstable, and the only way to obtain stable power is from the grid. But here is the logic to Audi’s claim. They say that the electricity they use for their e-gas plant is about the same as electricity from renewable energy sources. The company says that Audi buys electricity when electricity prices in Germany fall. Audi only operates its e-gas plant when the wholesale electricity price is 3-5 yen / kWh. According to Audi, when the wholesale price of electricity is low, the ratio of electricity from renewable energy in the grid increases to around 90%. The company says that taking electricity from the grid at that time is effectively equivalent to using renewable energy. In fact, looking at the share of renewable energy in the wholesale electricity price market reveals that when renewable energy is above 60%, wholesale electricity prices are also cheaper.Grids and electricity prices in Germany underpin Audi’s logic
Electricity price in Japan is basically fixed, but in Germany it is natural for the electricity price to fluctuate. The higher the demand, the higher the price is. However, the price drops at night and on weekends when demand is low. Germany’s electricity administration also has a role in lowering electricity prices when renewable energy occupies a higher share. In Germany, the law stipulates that renewable energy enjoys priority. That is, when the supply and demand balance in the system is disrupted and electricity becomes surplus, the first thing to be removed from the system is thermal power plants. If adjustment is still difficult, the last thing to be removed from the system is renewable energy. A way to reduce surplus power from the grid is to lower prices. Conversely, when the price is low, excess power is generated in the grid. That is, when thermal power plants are removed from the grid, the share of renewable energy increases. Audi uses the electricity at that time for 3-5 yen / kWh.Audi e-gas plant’s carbon dioxide
Next to the Audi e-gas plant (Werlte) is a biogas plant from which carbon dioxide is derived. Wind power is the number one source of renewable energy in Germany, followed by biogas and solar power. Germany has more than 10,000 biogas plants for methane fermentation. Livestock dung, such as that of cattle and pigs, is the raw material. For this reason, biogas plant operators are usually farmers. Biogas is a mixed gas composed of about 60% methane and about 40% carbon dioxide. If mixed biogas were used to power automobiles, its output would not enough, so carbon dioxide is separated and removed at a factory called an upgrade factory to convert it to high-purity methane. While methane is stored, the separated and removed carbon dioxide is released into the atmosphere. If this carbon dioxide could be reused, it would lead to carbon neutrality. That’s where Audi came in. The automaker uses surplus carbon dioxide, a by-product of methane fermentation, for methane (e-gas) production. There is no doubt that biogas is a good source of carbon dioxide, but fossil fuel-derived carbon dioxide is not bad either. For example, let’s suppose you do 100 jobs with fossil fuels and gain 100 carbon dioxide. If you reuse this carbon dioxide for methanation, you can do 100 more jobs. In other words, for 200 jobs, only 100 carbon dioxide is emitted. In brief, a single use of methanation can reduce carbon dioxide by 50%.Japan tests the world’s first simple carbon recycling system
As mentioned earlier, methanation is an old technique discovered by French chemist Sabatier in the early 1900s. In Japan, 26 years ago in 1993, Professor Koji Hashimoto, currently Emeritus Professor of Tohoku University, announced the Global Carbon Recycling Initiative. In 1995, a demonstration plant was installed on the roof of Tohoku University to recycle carbon dioxide. It combines a solar panel with a methane generator, an electrolyzer that generates hydrogen, and a burner that burns with oxygen (only emits carbon dioxide and water). Although it was a simple carbon-neutral device, Professor Hashimoto has demonstrated for the first time in the world that a real carbon-recycling system is possible. Many of Professor Hashimoto’s students, most who succeeded in methanation research, were employed by Hitachi Zosen. As a result, Hitachi Zosen has become a world leader in this field.R&D of methanation assumes worldwide penetration
Professor Hashimoto's methanation development had a firm idea. One is that no precious metals are used, and the other is that it is low-tech. Metals that can be mined anywhere can be used by anyone, making them practical for worldwide use. In light of Professor Hashimoto’s ideas, FCEV, a high-tech cluster using platinum, was absurd. When people ride FCEVs, precious metals are depleted from the earth. There are several catalysts to achieve methanation, but Hitachi Metals uses nickel, zirconium, calcium, and manganese. For this reason, commercialization can be cheap.Japan’s hydrogen is too expensive
In Germany, about 5 kWh of electricity is required to produce 1 Nm3 of hydrogen. If we calculate at the lowest price of 3 yen/kWh, the lowest price for which Audi procures electricity, it would cost 15 yen to make 1Nm3 of hydrogen in Germany. On the other hand, according to Japan’s Feed-in Tariff (FIT), the purchase price of onshore wind power is 20 yen/kWh. In other words, it would cost 100 yen to make 1Nm3 of hydrogen using renewable energy in Japan. The Japanese government has set a target price for hydrogen at 20 yen / Nm3, but it is currently five times the target. Achieving the target price will take a long time. Moreover, Germany is already generating hydrogen under 20 yen/Nm3 at the moment.Construction cost of a methane plant is one fifth of a hydrogen plant
The cost required to build a 325Nm3/h methanation plant is about 300 million yen. The corresponding amount of hydrogen generation is four times, that is, 1,600 Nm3/h, and a hydrogen production plant of that scale costs 1.5 billion yen. This means that a methane plant can be built for one-fifth of the cost of a hydrogen plant. Furthermore, the installation cost of the filling station (natural gas station) is significantly lower for natural gas (methane) than for hydrogen. The installation cost of a hydrogen gas station is 500-600 million yen per site, while the installation cost of a natural gas station is about 50 million yen. Moreover, natural gas is easier to handle than hydrogen. The problem is not the cost of building a factory or station. However, raw material costs account for 80% of gas prices, electricity costs accounting for most of it. Therefore, the penetration of methanation depends on electricity costs. With electricity costs as high as in Japan, the path of wide-scale diffusion is hard to see. The world’s largest renewable energy powerhouse China When it comes to electricity costs, Marubeni's solar power plant in the United Arab Emirates comes to mind. The unit price of electricity of this plant is less than 3 US cents/kWh. It is cheaper in China, and it is like there is no longer a selling price. Looking at that aspect alone, China is already the world’s largest renewable energy powerhouse. However, there is no plan to connect to the grid, so most of the power is currently being discarded.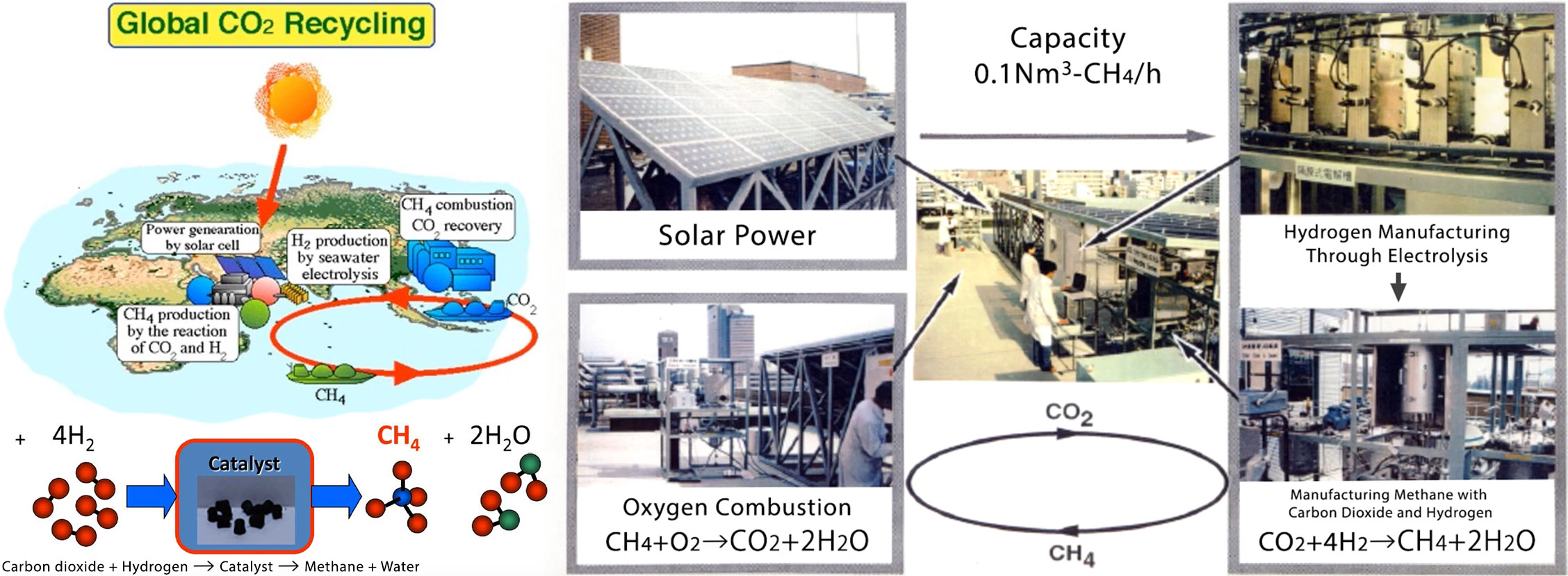