AAA weekly
2019-12-16
Copyright FOURIN, Inc. 2025
Gasoline Engines in Era of Electrification: Mass-made Pre-Combustion Chamber
Based on an interview with Shigeo Furuno (Senior Executive Director, SOKEN Inc.)
at SOKEN, Inc. (Nisshin City, Aichi Prefecture, Japan) on November 5, 2018)
Considering zero CO2, gasoline engines in the era of electrification / hybridization will require lean burn, higher compression ratio and improved knock resistance than ever before. At the same time, systemization may be easier. The role and specifications required for engines are changing due to electrification so the issues to be tackled are also changing. For this reason, engine-related suppliers and engineering consultant companies have proposed several new technologies. pre-combustion chamber is one of them.
FOURIN conducted an interview with Shigeo Furuno (Senior Executive Director, SOKEN Co., Ltd.) about the features and issues of the pre-combustion chamber and the possibility of mass production. Mr. Furuno is a former Toyota powertrain developer and is familiar with engine development trends in Japan and Europe.
The first time to use a pre-combustion chamber for a gasoline engine was the CVCC engine that Honda announced in 1972. At that time, the focus was on exhaust gas control in response to the US Muskie Law. However, pre-combustion chamber-type gasoline engines disappeared from the market after the appearance of the three-way catalyst. MAHLE announced the Turbulent Jet Ignition in the first half of the 2010s and its use in the motor sports field has gained popularity. In recent years, German engineering consulting firm IAV has proposed that it can also be applied to mass-produced vehicles.
The reason why the pre-combustion chamber has attracted attention again is that a high compression ratio can be realized relatively easily. When the air-fuel mixture is ignited in the pre-combustion chamber, high-pressure flames enter the main combustion chamber through multiple small openings. This realizes volume ignition in the entire main combustion chamber, shortens the combustion period and does not give time for knocking. It increases knock resistance and achieves high compression ratio. IAV has also pointed out the good compatibility between the Miller cycle of the intake valve’s early closing, the cooled EGR and the pre-combustion chamber. Depending on the combination, fuel efficiency can be improved by 1 to 11%.
On the other hand, the problem of cooling loss still remains an issue of the pre-combustion chamber. Cooling loss in the vicinity of the wall of the pre-combustion chamber or in the vicinity of the wall leading to the main combustion chamber adversely affects fuel consumption. In the case of motor sports, the problem of cooling loss is relatively minor because the operating range of the engine is concentrated in high-load areas. However, for mass-produced vehicles, the time for idle operation and light load operation is long, so the adverse effects of cooling loss are more pronounced.
In Mr. Furuno's view, a hybrid vehicle that can compensate for these light-load areas with motor drive is likely to be mass-produced with a pre-combustion chamber. In that respect, challenges to tackle are less compared to ultra-high fuel injection pressure, which has many issues to overcome such as sealing.
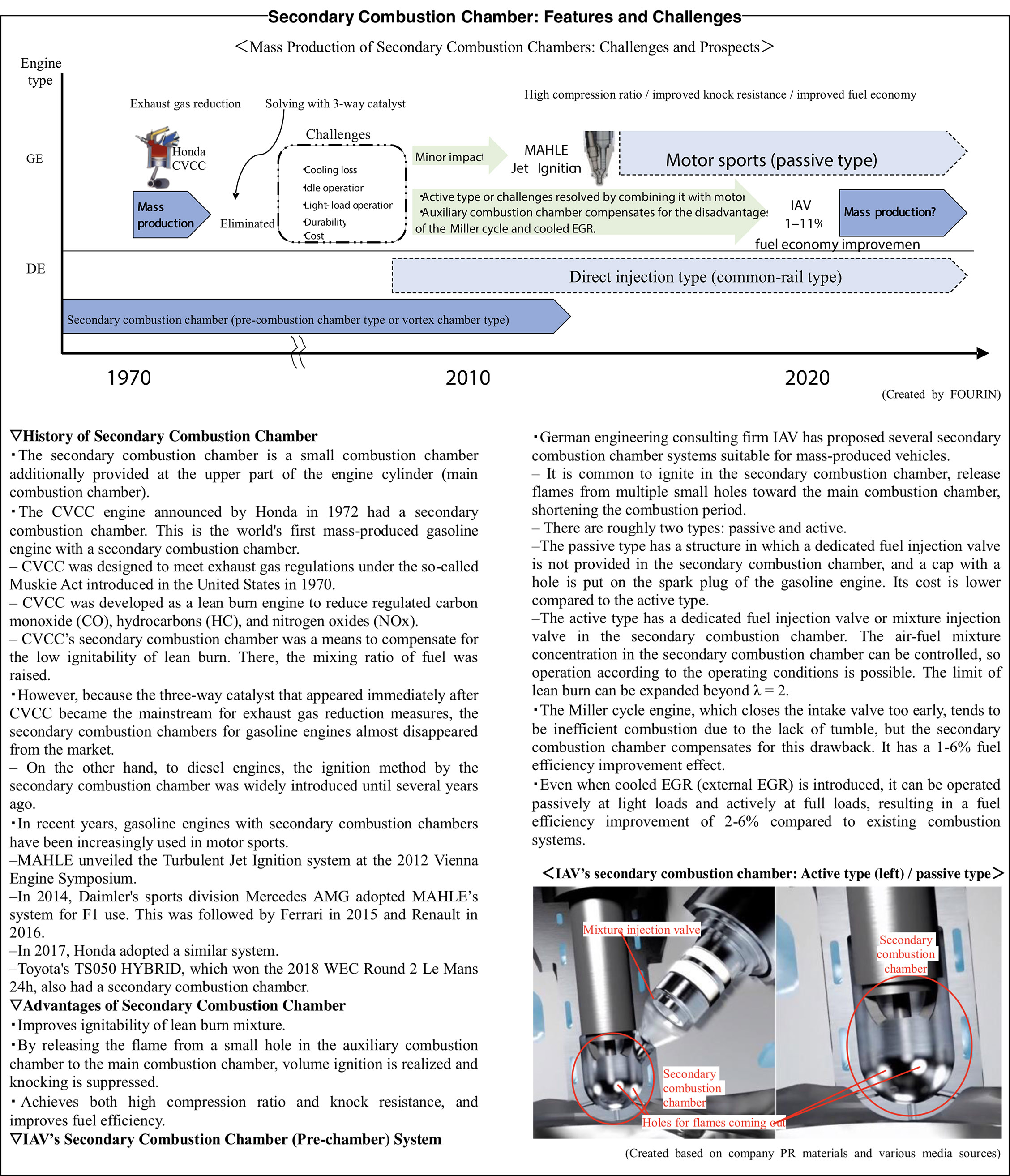
Cooling loss problem peculiar to the pre-combustion chamber
The cooling loss is a phenomenon in which combustion heat escapes to the wall surface of the pre-combustion chamber or the wall surface of the main combustion chamber while it moves from the pre-combustion chamber. Of particular concern is the temperature difference (ΔT) between the wall surface and the combustion gas. It is called delta (Δ) T. If there is no ΔT, there is no cooling loss. To put it simply, if ΔT = 0, no cooling loss occurs even if the combustion gas moves from the narrow pre-combustion chamber to the wide main combustion chamber. The pre-combustion chamber prevents ΔT = 0. In particular, ΔT increases at the exit from the pre-combustion chamber. The exit portion is narrow, so the flow velocity of the combustion gas passing through increases. As the flow rate increases, the heat transfer coefficient increases so cooling loss tends to increase. This is because the heat transfer coefficient from the high-temperature gas body to the wall surface is almost proportional to ΔT and the flow velocity.
Reasons why mass production of the pre-combustion chamber is difficult 2
There is another reason why mass production of the pre-combustion chamber is difficult apart from cooling loss. Depending on which method is used, for example, in the case of the passive type (a system that sucks the air-fuel mixture into the pre-combustion chamber, ignites it, and injects the flame into the main combustion chamber), there is no problem near maximum output. However, in the idling or light load region, the air-fuel mixture in the pre-combustion chamber cannot be scavenged sufficiently. This interferes with idling.
pre-combustion chamber becoming mainstream in motor sports
Despite their shortcomings, pre-combustion chambers have been adopted in the world of motorsports such as Formula 1 (F1) and World Endurance Championship (WEC). In motorsports, engines are mostly operated at maximum power. Therefore In this part, ΔT is minimal. This is because the wall temperature is high in the first place. In other words, engines used in motorsports have not completely solved the problem of cooling loss, but this problem is relatively small compared to that of mass-produced vehicle engines. While idling and light load driving frequently occurs with mass-manufactured cars, these issues can be ignored when it comes to motorsports engines.
There is another reason why a pre-combustion chamber is used in motorsports. In motorsport engines, it is easy to set the compression ratio high, so knocking can be suppressed by flame injection from the pre-combustion chamber. Although there is a problem of cooling loss, the merit obtained is larger because the thermal efficiency is increased by increasing the compression ratio. In addition, motorsports is more apt to adopt a pre-combustion chamber than mass-produced vehicles in terms of cost and durability.
Types of pre-combustion chambers (Active and passive)
There are two main types of pre-combustion chambers. Active type and passive type. Active type means that there is a dedicated fuel injection valve or air-fuel mixture injection valve in the pre-combustion chamber.
The passive type is a system in which the air-fuel mixture is sucked into the pre-combustion chamber, and there is no dedicated fuel injection valve in the pre-combustion chamber. More simply put, it's like a typical gasoline engine spark plug with a perforated cap.
One of the merits of the active type is that, as described above, air-fuel mixtures having different concentrations can be used in the pre-combustion chamber and the main combustion chamber. On the other hand, the concentration of the air-fuel mixture of the passive type is unchanged. However, by having a pre-combustion chamber, the internal pressure can be immediately increased.
By letting high-pressure combustion gas enter through holes from the pre-combustion chamber to the main combustion chamber, many flame nuclei are formed in the main combustion chamber and so-called volume ignition occurs. Of course, the benefits of volume ignition can be gained even with the active type. This phenomenon of volume ignition is another reason that pre-combustion chambers have attracted attention in recent years.
Volume ignition generated in the pre-combustion chamber
Thanks to volume ignition, the flame reaches the cylinder wall at once, just like the high-pressure injection of a diesel engine. This is effective in suppressing knocking. Knocking occurs in a regular engine because the unburned portion of the air-fuel mixture remains in the vicinity of the bore (near the cylinder wall surface). When the unburned remaining air-fuel mixture becomes hot, it ignites which results in knocking.
Volume ignition shortens the combustion period. It is shorter than that of a regular gasoline engine without a pre-combustion chamber. Volume ignition by the pre-combustion chamber gives no time to knock. Looking at the combustion of the air-fuel mixture, cold flame reaction always has a time period before the hot flame reaction, that is, the ignition delay time is not zero. With the Livengood-Wu integration, the ignition delay time is integrated over the temperature, and when the value becomes 1, it is said that knocking occurs. As for volume ignition, it burns out before Livengood-Wu integral value becomes 1.
High pressure fuel injection in gasoline engines
It doesn’t mean that there is no way to reduce the Livengood-Wu integral value to less than 1 using only a direct injection injector without using a pre-combustion chamber. One of them is to increase the fuel injection pressure. For example, Mazda’s newly developed gasoline engine SKYACTIV-X has a very high injection pressure and a short injection time. Thereby, the timing of injection can be delayed to the last moment, and the time until the air-fuel mixture burns out by flame propagation can be shortened.
If it is slow, heat energy will continue to be applied to the unburned mixture and knocking will occur; however, such time will not be given.
However, it is not easy to achieve the same high pressure as a diesel engine with a gasoline engine. This is because the gasoline engine has a lower fuel viscosity than light oil, which causes new problems with seals and high-pressure fuel pumps.
A pre-combustion chamber is one solution that achieves both high compression ratio and knocking resistance by a method different from ultra-high injection pressure.
Please
register or subscribe to view this report for free.
If you’re already a subscriber, sign in.
Credit card information is not needed for free trial registration.
You are eligible to view one report for free.
Additional reports require subscription.